Construction is a rapidly evolving industry and with the introduction of new materials and techniques, building structures have become faster, more efficient, and cost-effective. In this article, we will take a closer look at two such construction technologies – Mivan technology and precast concrete technology – and compare their respective benefits and drawbacks, as well as cost comparisons.
Mivan Technology
Mivan technology is a type of aluminum formwork system used for constructing high-rise buildings and large-scale structures. The system is designed to eliminate the need for traditional concrete formwork, which can be time-consuming and labor-intensive. Instead, Mivan technology uses lightweight aluminum formwork that can be quickly assembled and disassembled, reducing the time and labor needed for each construction cycle.
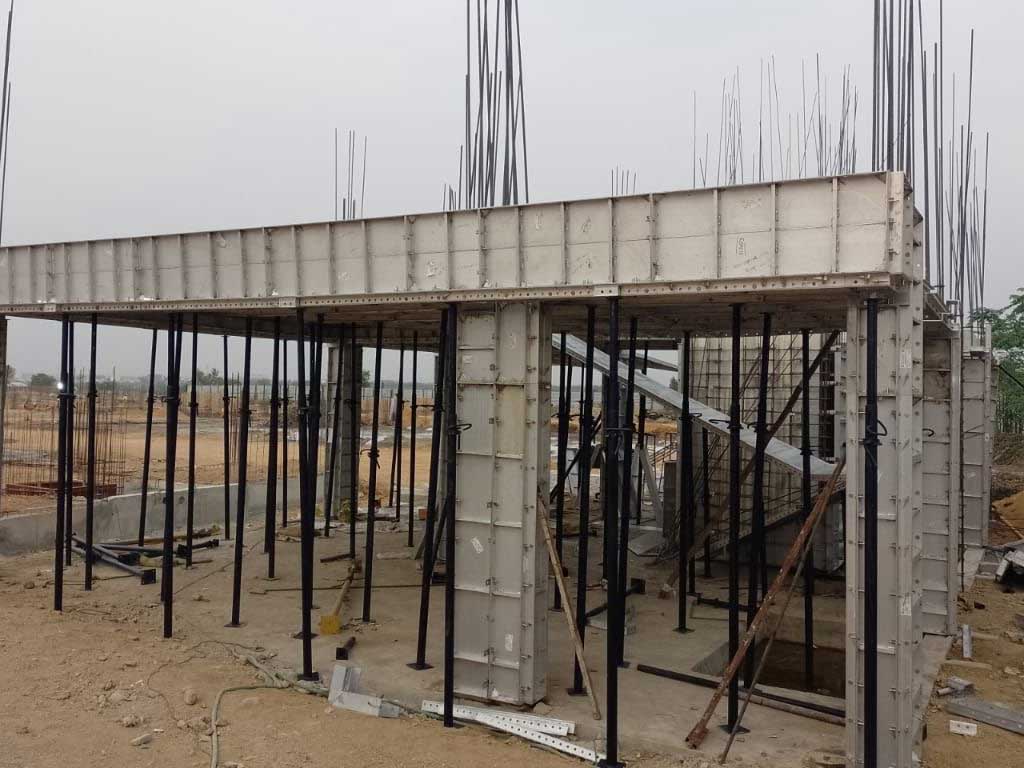
Precast Concrete Technology
Precast concrete technology involves casting concrete components in a controlled environment and then transporting them to the construction site for assembly. This method of construction is commonly used for buildings, bridges, and infrastructure projects.
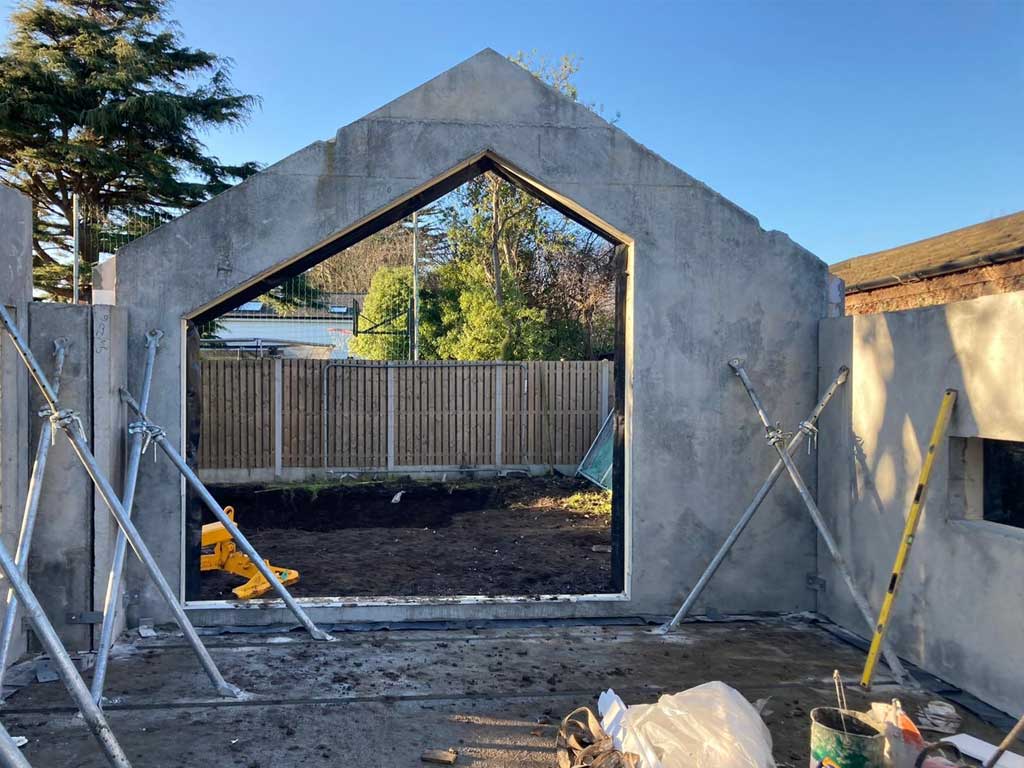
Credit : Hi Therm Homes – site photo
Comparison- Mivan Technology vs Precast Concrete Technology
Now let us compare both these construction technologies with respect to various aspects like speed, quality, cost, and labor requirement
Speed
Both Precast and Mivan technologies are much faster than the conventional cast-in-situ construction. In the case of Precast, the elements are manufactured in a factory or on site and then joined and erected at site using cranes thereby reducing the time required for construction. In the case of Mivan, the lightweight Aluminum formwork can be quickly assembled and disassembled on site, which in turn reduces the time needed for construction. However, there are still some differences when these technologies are compared with each other:
Precast Concrete | Mivan |
---|---|
Once the design and BOQ are in place, the precast elements can be manufactured and cured very fast under controlled factory settings. | Since concrete is poured into the formwork at site, the curing time is as long as the conventional construction method. This makes Mivan slower than precast when it comes to the time taken for construction. |
Transportation of precast elements is a delicate job and must be handled carefully. Therefore, there could be delays due to the time taken in transporting the precast elements to site, thereby causing an overall delay in construction. For large projects, however, precast elements can be cast on site, and this drawback can be avoided. | There is no transportation of elements involved in this case. Everything is done on site. |
Overall, Precast construction is faster than Mivan when it comes to large projects where the precast elements can be cast on site itself.
Quality
Both the technologies offer a high-quality finish and there is no need to spend extra time or additional amounts of money on finishing.
Labor
Both the technologies require less labor as compared to conventional construction methods but again, between the two, the amount of labor needed for precast is relatively small compared to Mivan.
Cost comparison
The initial setup cost for Mivan as well as Precast is large. However, in general, Mivan technology can be more expensive due to the cost of the aluminum formwork and associated equipment. Precast concrete technology can also be costly, especially if transportation costs are high but again, as mentioned above, for very large projects, precast elements can be cast on site, thereby cutting on the significantly high transportation cost and making it a more viable alternative economically.
Other considerations
Mivan technology is limited in the size of structures it can construct, as the aluminum formwork has weight limitations while there is no such constraint with Precast concrete technology.
From the above comparison, it is clear that Precast Concrete technology has a definite edge over Mivan technology and more so, when it comes to large projects.
FAQs: Mivan Technology vs. Precast Concrete Technology in Construction
Both Mivan and Precast technologies accelerate the construction process compared to traditional methods. Precast has an edge in speed, especially for large projects where elements can be cast on-site, avoiding transportation delays. Mivan’s on-site concrete pouring and curing extend its construction timeline, making Precast generally faster.
Both Mivan and Precast Concrete technologies provide a high-quality finish, eliminating the need for additional time or money on finishing work. The quality aspect is comparable between the two, with neither having a significant advantage over the other in this regard.
Both technologies reduce the labor requirement compared to traditional construction methods. However, Precast Concrete typically requires less labor than Mivan, making it more efficient in terms of manpower utilization.
The initial setup costs for both Mivan and Precast Concrete are significant. Mivan may incur higher costs due to the price of aluminum formwork and equipment. Precast Concrete can also be costly, particularly with high transportation costs, but for large projects where elements are cast on-site, it can be more economically viable.
Mivan technology has size limitations due to the weight constraints of aluminum formwork. Precast Concrete technology does not have such limitations, making it more versatile for constructing larger structures.