Precast concrete construction continues to gain popularity due to its numerous benefits, including faster construction, improved quality control, and reduced on-site labour. However, the success of any precast project hinges on the reliability and effectiveness of the connections between the individual precast elements. This article delves into the world of precast connections, exploring types, applications, and considerations to help you understand and choose the most suitable options for your project.
Demystifying Precast Connections
Precast connections, also referred to as connections between precast elements, are the crucial junctions that ensure structural integrity and transfer loads within a precast concrete construction.
Connections categorized by their construction method
Dry Connections: Employing mechanical fasteners like bolts, dowels, and inserts, dry connections offer fast installation and clean work. However, they rely heavily on precise installation and may have limitations in fire resistance.
- Fast and clean installation: Dry connections can be completed quickly and without the mess associated with wet concrete.
- Easy on-site adjustments: Minor adjustments can be made during installation to ensure proper alignment.
- Reusable connections: Some types of dry connections, like bolted joints, can be disassembled and reassembled if necessary.
However, dry connections come with certain drawbacks:
- Precise installation is critical: These connections rely heavily on the accuracy of fastener placement and tightening, which necessitates skilled labour. Improper installation can compromise the connection's strength and performance.
- Limited fire resistance: Dry connections might not provide the same level of fire protection as wet connections. This is crucial to consider, especially in projects with specific fire safety requirements.
Wet Connections: These connections use poured concrete in combination with mechanical fasteners to create a strong and permanent joint. Their advantages include:
- Strength and durability: Wet connections offer greater load-bearing capacity and improved resistance to fire and other environmental factors.
- Adaptability: They can be customized to accommodate various load demands and site conditions.
Wet connections, while advantageous, also present some challenges:
- Extended installation time: Since the concrete needs to cure properly, wet connections lengthen the overall construction timeline compared to dry connections.
- Skilled labour requirement: Proper mixing, placing, and finishing of the concrete demands experienced personnel. This can impact the project cost and schedule if skilled labour is limited.
Hybrid Connections: Sometimes, a combination of dry and wet methods is used for specific connection needs. This can involve using dry connections for initial alignment and stability, followed by grouting, or embedding them in concrete for added strength and fire resistance.
Types of Connections by Location
Beam-to-Column Connections:
- Bolted connections: These are widely used for their simplicity and ease of installation. Bolts are inserted through pre-drilled holes in the beam and column and tightened to create a secure joint. They are suitable for moderate loads.
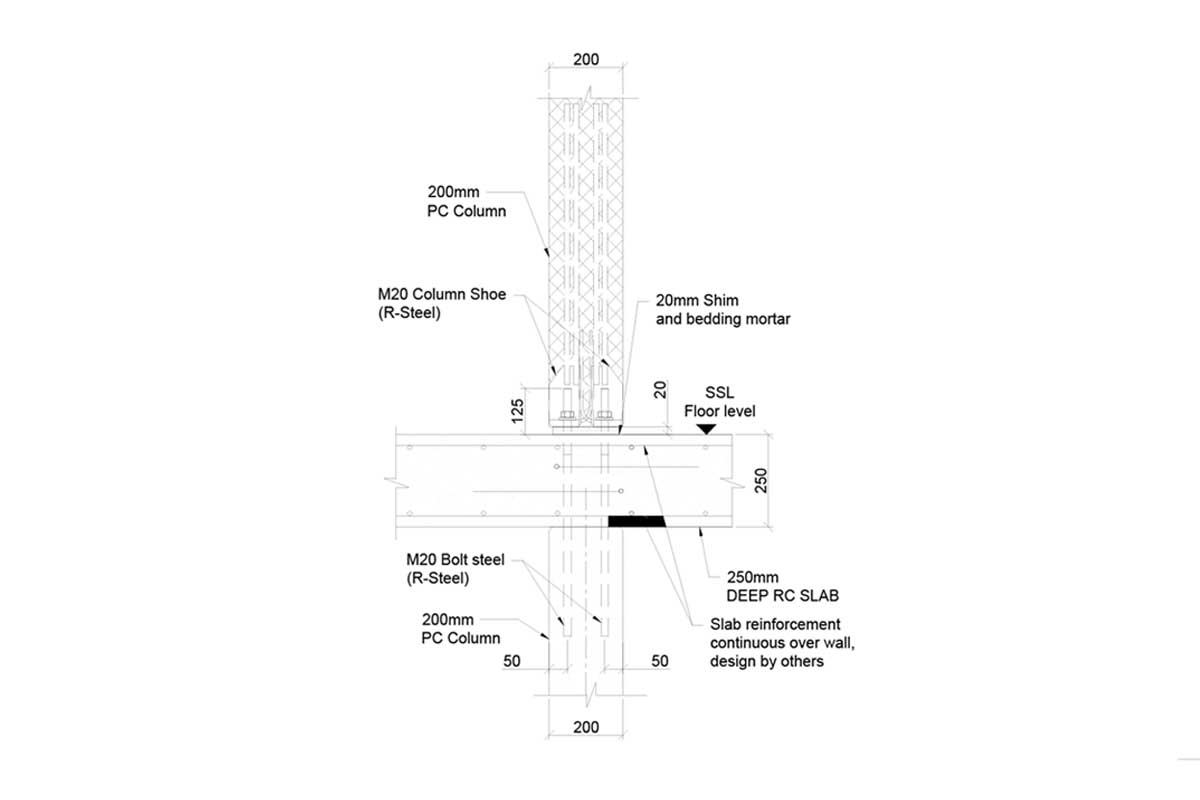
Column to column connection - Bolted
- Welded connections: This method offers a high-strength connection by welding steel plates embedded in the beam and column elements. It is preferred for situations requiring greater load capacity and is often used in seismic zones.
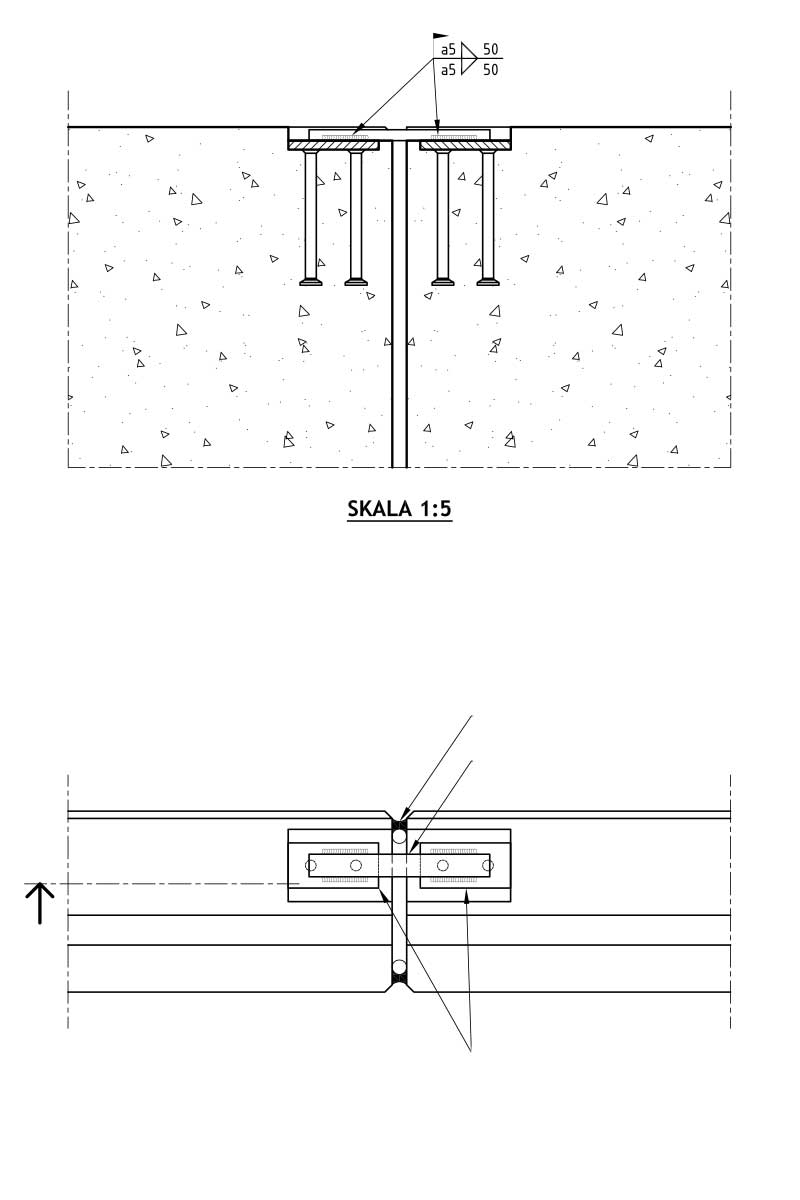
Welded connection
- Grouted connections: Here, the space between the beam and column is filled with grout after the initial positioning with bolts or dowels. This method offers good strength and fire resistance without the heat involved in welding.
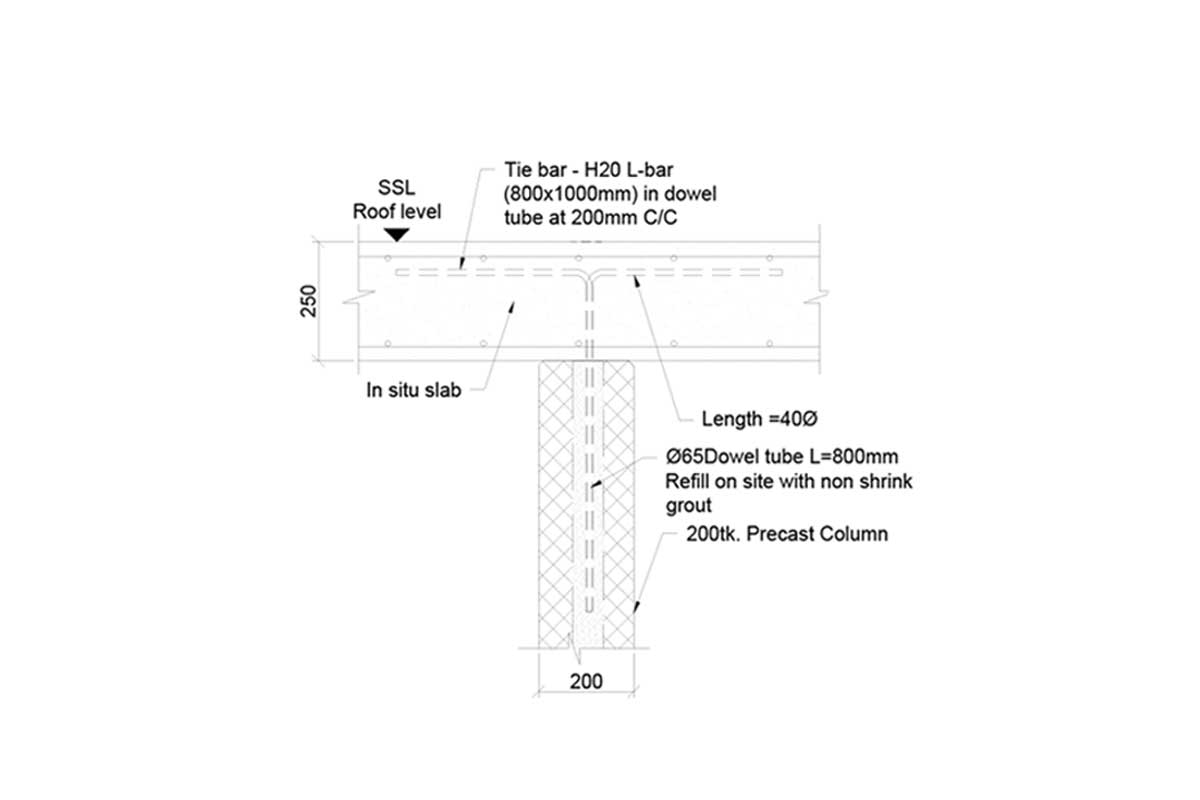
Grouted connection
- Dowelled connections: These connections utilize precast concrete elements with embedded steel dowels that fit into corresponding holes in the connecting element. Grout is then used to fill the remaining space, creating a strong and durable joint.
Column-to-Column Connections:
- Sleeved connections: These involve placing a precast column section with a larger diameter over a smaller section below. The gap between the columns is filled with grout to create a continuous and strong connection.
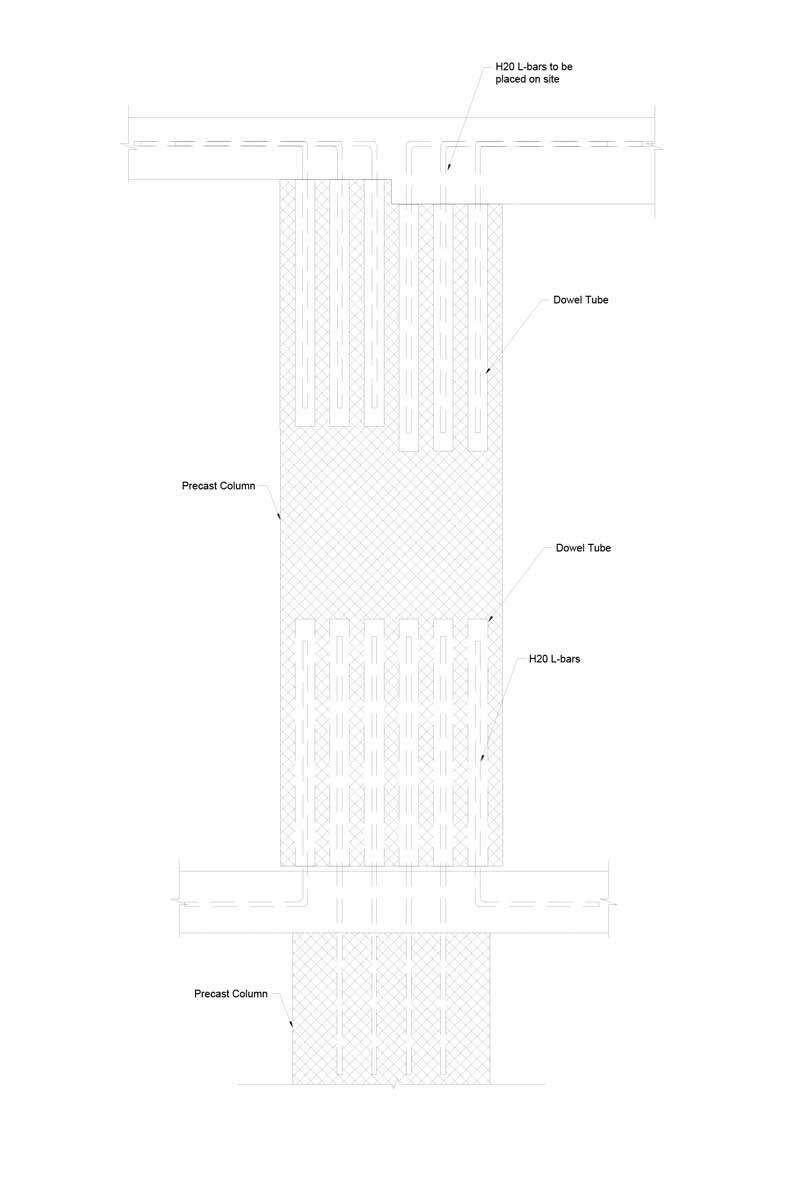
PC column to column connection - Sleeved
- Grouted connections: Similar to beam-to-column connections, grouting can be used to connect precast columns directly, offering good load transfer and fire resistance.

Precast column grouted connection
- Bolted connections: In some cases, bolted connections may be sufficient for column-to-column joints, especially when dealing with lighter loads.
Wall Panel Connections:
- Dry connections: Tongue-and-groove joints, along with mechanical fasteners like clips or anchors, can be used to connect wall panels efficiently in a dry manner.
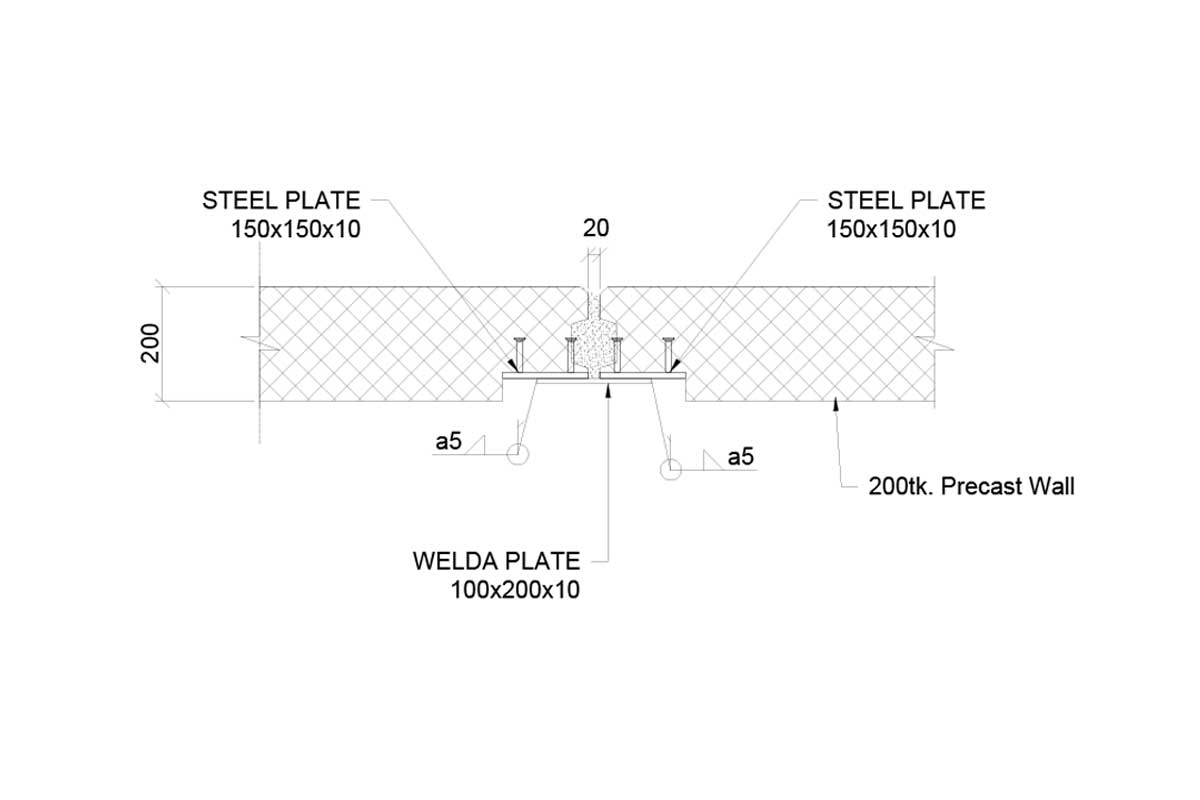
Dry connection
- Wet connections: Precast wall panels can be connected using poured concrete along the joints, offering improved sound insulation and fire resistance.
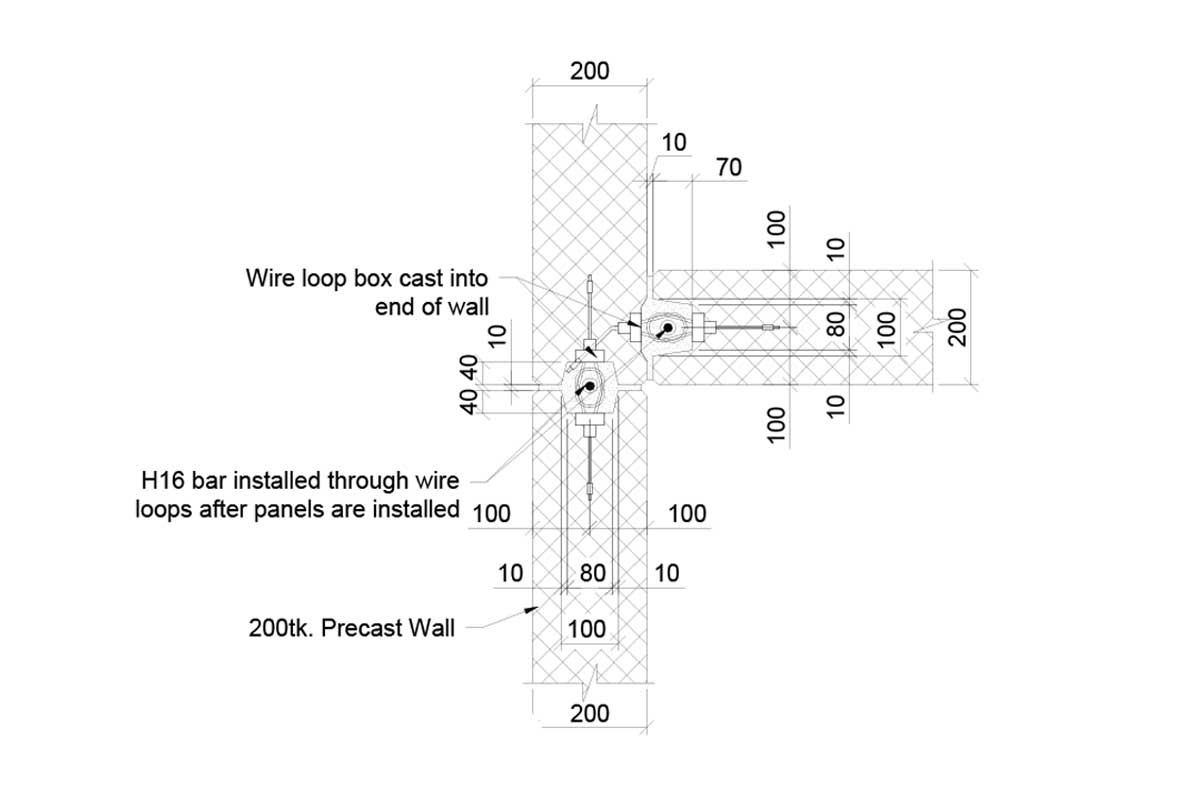
Wet connection
Floor-to-Beam Connections:
- Shear keys: These are concrete keys cast into the beam elements that interlock with corresponding grooves in the precast floor slabs, preventing horizontal movement and ensuring composite action.
- Post-tensioning: This technique uses high-strength steel tendons to apply compressive stress to the floor slabs after they are placed on the beams. This improves the overall strength and stiffness of the floor system.
Choosing the Right Precast Connections:
Selecting the most suitable ones for your project requires careful consideration of various factors:
- Load demands: The connection needs to be able to safely transfer the intended loads within the structure.
- Fire resistance requirements: Some projects require connections with specific fire resistance ratings.
- Construction speed and site constraints: Dry connections can be faster to install, while wet connections may require additional planning and curing time.
- Budgetary considerations: Costs associated with materials, labour, and complexity of installation need to be factored in.
Designing proper precast connections is crucial for the structural integrity of your project. By understanding the different types, their characteristics, and suitability for various locations, you can make informed decisions. Consulting with experienced engineers is essential for project-specific analysis and selection of the most appropriate connection methods. By incorporating proper detailing and rigorous quality control, you can guarantee a strong, reliable, and efficient precast concrete structure.
Essential Guide to Precast Connections: Your FAQs Answered
Yes, precast connections can be used in various parts of a building, including beam-to-column connections, column-to-column connections, wall panel connections, and floor-to-beam connections. Each connection type is designed to meet the specific requirements of its location within the structure, ensuring effective load transfer and structural integrity.
Dry connections offer fast installation and clean work but require precise installation and may have limitations in fire resistance. Wet connections provide greater strength and durability, adaptability to various load demands, and improved fire resistance but require more time for installation due to the curing process and demand skilled labor.
Choosing the right type of precast connection depends on several factors, including the load demands of the structure, fire resistance requirements, construction speed, site constraints, and budgetary considerations. It’s essential to analyze these factors carefully and consult with experienced engineers to select the most suitable connection method for your project.
The main types of precast connections include dry connections, which use mechanical fasteners like bolts and dowels; wet connections, which involve the use of poured concrete along with mechanical fasteners; and hybrid connections, which combine both dry and wet methods to meet specific connection needs.
Precast connections refer to the junctions between individual precast concrete elements within a construction project. These connections are crucial for ensuring the structural integrity of the building, as they are responsible for transferring loads and maintaining the overall stability of the structure.