In the construction industry, there is a growing trend towards utilizing precast technology for a variety of projects and there are many good reasons for this. This technology offers several advantages like faster construction times, reduced costs, improved quality, and enhanced durability. With the continued development of 3D BIM modelling tools and advanced precast manufacturing techniques, it is becoming increasingly viable to replace the in-situ construction method with precast technology, benefiting both – construction companies and their clients.
Project Overview
ITB is a leading construction company in Nigeria that specializes in providing high-quality construction services. The company was contracted to construct a Data Center and a Generator House for a client. Being well apprised of the numerous benefits that precast technology offers, they decided to use precast concrete elements for floor slabs & beams with the intent of reducing construction time and minimizing labor requirement.
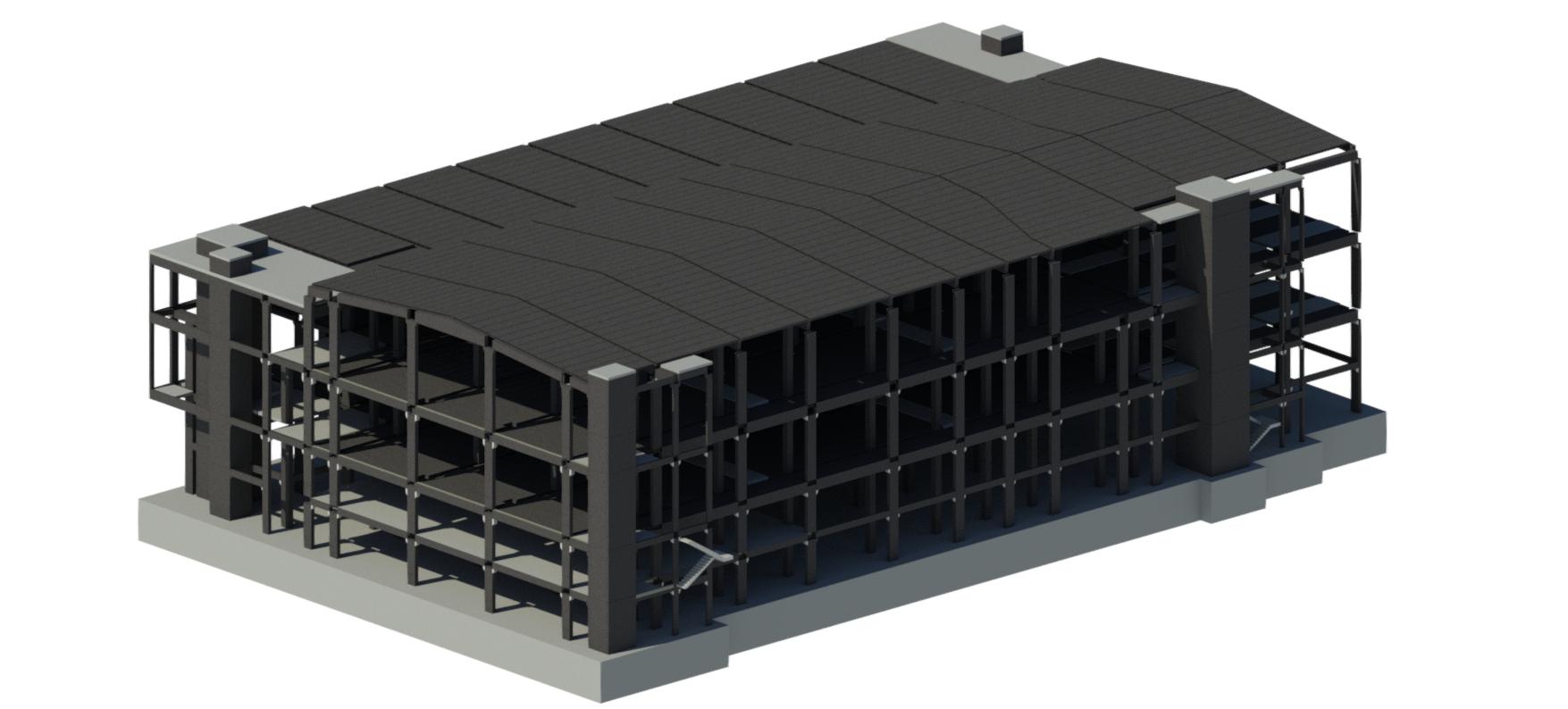
Revit model
Challenges
Despite the obvious advantages, the decision to go with precast came with some challenges as it was the first time ITB was opting for precast elements for a Data Center kind of a requirement. The major challenge was designing the floor slabs to withstand a heavy load of 20 kpa. The floor slabs had to be designed to support the weight of server racks and other heavy equipment. Some hollow core & beam spans went up to 9.5 meters, which made it difficult for them to find the right design that could meet the load requirements and maintain the structural integrity of the building.
Solution
To overcome this challenge the ITB Nigeria team used prestressed hollow core slabs and beams. The precast concrete elements were designed using IMPACT 3D BIM modelling, which made it easier to visualize the structure and identify any potential issues before construction began.
As per the design requirements, the project incorporated hollow core slabs with two different thicknesses: 250 mm and 360 mm with a width of 1200 mm. Prestressed reinforcement was placed in the hollow core to give the slab additional strength and rigidity. The beams were designed with a cross-section of 400 mm x 400 mm and a length of 9.5 m. The beams were also prestressed to provide additional strength and support to the floor slabs.
The hollow core slabs of 360 mm thickness were designed with a 75mm structural screed, while the 250 mm thick hollow core slabs were designed with a 50 mm structural screed, which provided additional strength and durability to the flooring system.
To match the strength of in-situ jointing systems, emulative joints were engineered for interconnecting the precast elements. This design approach guaranteed a seamless connection between the precast components and enhanced the structural integrity of the building.
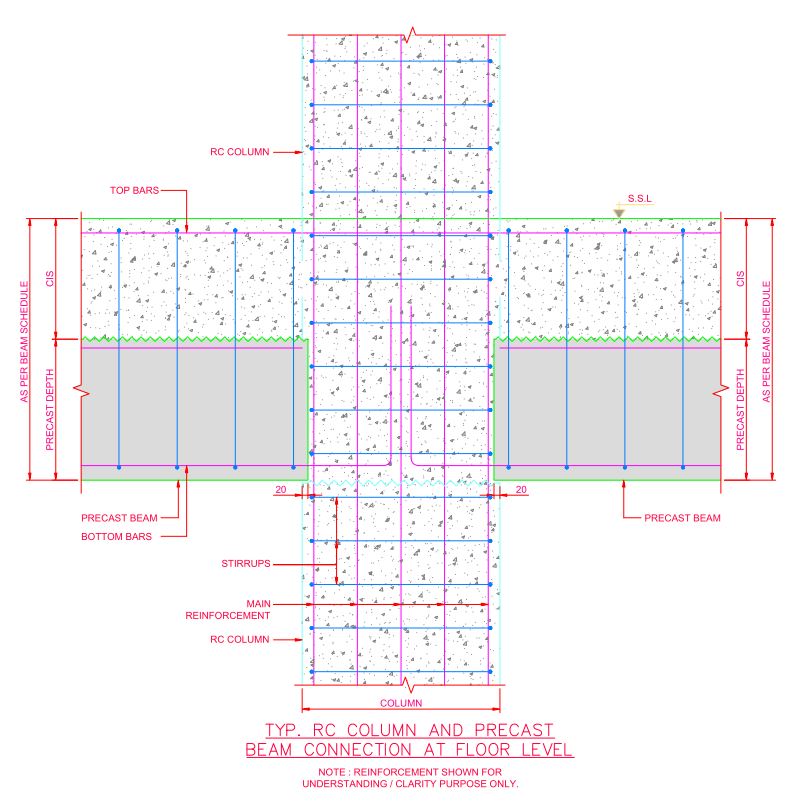
Emulative joints
Outcome
The use of prestressed hollow core slabs and beams proved to be an excellent solution for the ITB Nigeria team. The final structure was able to withstand the heavy load requirements of the data center, and the joints between the precast elements were seamless, making the structure more durable.
Benefits to the Client
The use of precast concrete elements provided several benefits to the client:
- Firstly, it allowed for a faster construction process, as the precast elements could be manufactured off-site while the site was being prepared. This helped to reduce the construction time, which in turn helped to save costs for the client.
- Secondly, the use of 3D BIM modelling helped to identify and address any potential issues before construction began. This helped to minimize any rework during the construction process, which again helped to save time and money for the client.
- Thirdly, the prestressed precast concrete elements provided a highly durable and reliable structure that met the load requirements of the data center. This ensured that the client could operate their IT equipment with confidence, knowing that the structure could withstand the weight and other demands of the equipment.
- There was reduced requirement of labor.
- The construction site was Clean and Safe.
Conclusion
The goal of completing the Hybrid Precast Structure Data Center with the required structural strength in a shorter time frame than traditional construction methods was successfully met with.
The advantage of 3D BIM modelling for structural analysis and error detection before commencing work at site was fully leveraged.