Bendcrete Skateparks specialize in making skateparks & scooter parks and have produced some of the most popular skateparks around the UK and Ireland using innovative designs. The tunnel was a part of a kids' play area to be developed with the idea of giving kids a first-hand experience of how it feels to crawl through an underground tunnel.
Bendcrete approached us with the idea, we deliberated whether to build the tunnel in precast or in-situ. We made detailed designs & drawings for both the options and shared them with the client. Finally, it was decided that this project should be a Hybrid Precast Structure; i.e, a combination of precast and cast-in-situ.
Preliminary ideation – some initial sketches shared by the client
The tunnel in its entirety has a total length of 55 meters and consists of 3 (three) sub tunnels – A, B & C with A and C. Based on the load data inputs, the thickness of the top slab, bottom slab and side walls was taken as 150 mm. The final agreed shape of the tunnel was as under
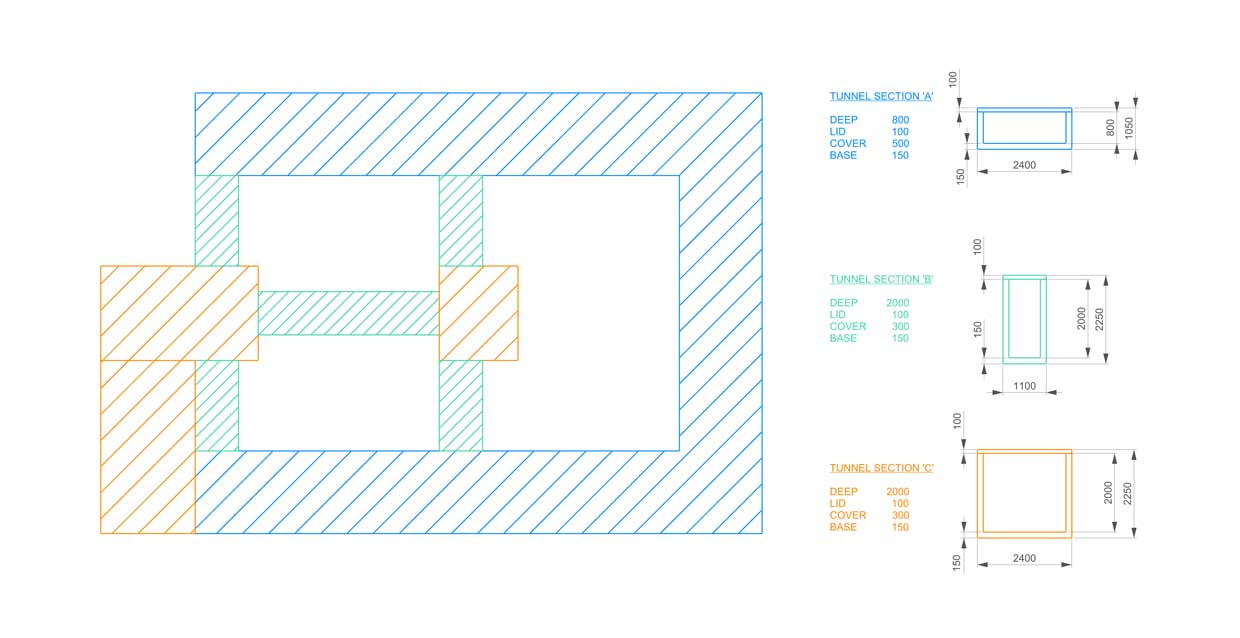
Additionally, the client also shared with us the following site-related inputs :-
- Soil load above the cave (acting on the roof)
- Lateral load on side walls due to backfill soil
- Uplift due to bottom Earth reaction
- Geotechnical data like soil type and soil retaining capacity
Based on these inputs, the structure was designed with 2D manual calculation with further validation in 3D using our proprietary FEA software – FEM Design.
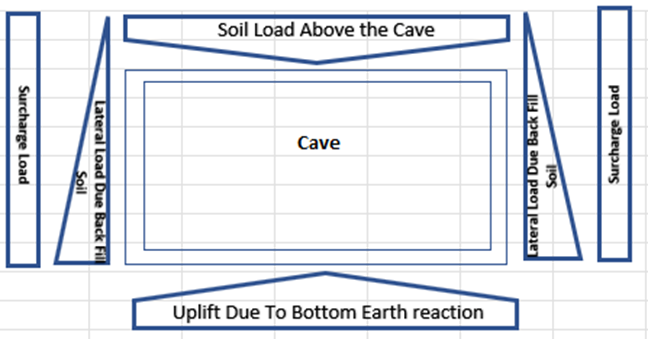
The additional benefit of using FEM Design was that we could get both directional Moments to check reinforcement design in both the directions – lateral & vertical.
Representative FEA for Tunnel A
As mentioned above, it was decided that the side walls would be cast-in-place, while the roof would be made of precast slabs. For Precast we needed to design connections to resist the force generated at joints and bends. Initially, the bottom slab was also decided to be made of three different elements and prefabricate each of them but because the project was getting delayed, the contractor decided to go for cast-in-place bottom slab and side walls with prefabricated top slabs, which are more convenient in case of maintenance in service stage.
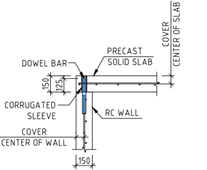
The client requested us to provide U-shaped Mesh with BBS (Bar Bending Schedules). StruEngineers used IMPACT RC for preparing RC drawings and bar bending schedules were automatically generated by the software, which eliminated potential errors of manual input of BBS.
StruEngineers submitted the final set of drawings to Bendcrete in 14 days from receiving the final inputs needed from client for Design and detailing.