Building Information Modeling (BIM) has become a widely used tool in the construction industry, transforming the way projects are planned, designed, and executed. BIM offers a wealth of benefits, from increased efficiency to improved quality, and the precast concrete industry is no exception. In this blog post, we will explore how BIM can be used to unlock the power of precast production planning, maximizing efficiency and quality.
What is BIM in Precast Production Planning?
BIM is a digital representation of the physical and functional characteristics of a building or structure, including its geometry, spatial relationships, and other relevant information. In precast production planning, BIM is used to create a detailed 3D model of a precast element, such as a wall panel or a beam. The model includes all the necessary information for the production process, such as reinforcement, embedded items, and connections.
By using BIM in precast production planning, the precast manufacturer can visualize the element in 3D, analyze it, and optimize the production process. The use of BIM can also help reduce errors and conflicts, as all the information is available in one place, making it easier for different teams to work together.
Maximizing Efficiency with BIM in Precast Production Planning
BIM can bring significant benefits to the precast production process by maximizing efficiency. By using BIM, precast manufacturers can optimize their production process by reducing waste, increasing accuracy, and minimizing errors.
Reduce Waste
One of the significant benefits of using BIM in precast production planning is reducing waste. BIM can help manufacturers optimize the use of materials by calculating the exact amount of material needed for a precast element. This can help reduce waste and save money. By reducing waste, precast manufacturers can also contribute to sustainable construction practices, reducing the environmental impact of construction projects.
Increase Accuracy
BIM can also help increase the accuracy of precast elements. By providing a detailed 3D model of the precast element, manufacturers can ensure that each element is consistent and of high quality. The use of BIM can also aid in quality control and inspection, as the 3D model can be used as a reference point to ensure that each element is produced to the same standard.
Minimize Errors
BIM can help prevent errors in precast production planning by identifying and resolving conflicts between different components before they occur. This can help reduce the risk of delays and additional costs during production. By using BIM, precast manufacturers can identify potential issues in the production process and make adjustments before production begins, reducing the likelihood of errors.
Improving Quality with BIM in Precast Production Planning
BIM can also improve the quality of precast elements by providing detailed information about the design and production process. BIM can help precast manufacturers:
Visualize the Precast Element in 3D
BIM provides a detailed 3D model of the precast element, allowing manufacturers to visualize it and identify any potential issues before production begins. This can help improve the quality of the precast element by ensuring that any issues are addressed before production begins.
Analyze the Precast Element
BIM can help manufacturers analyze the precast element by simulating its behaviour under different conditions, such as load, temperature, and moisture. By analyzing the precast element, manufacturers can ensure that it is suitable for its intended purpose and will perform as expected.
Optimize the Production Process
BIM can help manufacturers optimize the production process by identifying the most efficient way to produce the precast element, considering factors such as material, labor, and equipment. By optimizing the production process, manufacturers can reduce production time and costs, while also improving the quality of the precast element.
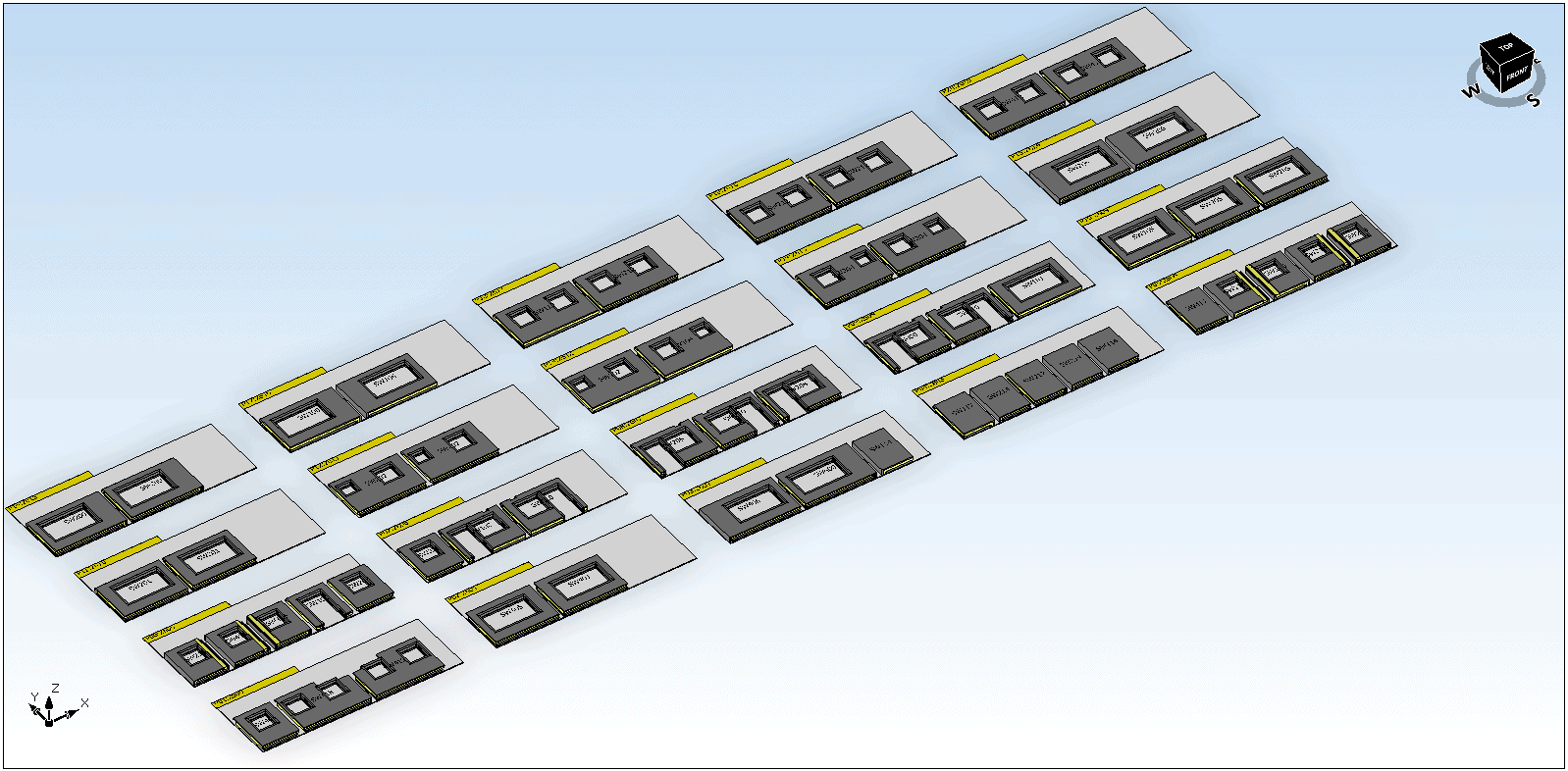
Challenges and Solutions
While BIM offers many benefits to precast production planning, there are also some challenges that need to be addressed. One of the biggest challenges is the need for collaboration and coordination between different teams involved in the production process, such as architects, engineers, and contractors.
To address this challenge, precast manufacturers need to develop effective communication strategies and protocols to ensure that all stakeholders are working together efficiently. This can involve regular meetings, shared platforms for information exchange, and clear documentation of decisions and actions.
Another challenge is the need for specialized knowledge and skills to use BIM effectively in precast production planning. This can include knowledge of software programs, technical skills, and a deep understanding of the precast manufacturing process.
To address this challenge, precast manufacturers can invest in training and development programs for their staff, providing them with the skills and knowledge needed to use BIM effectively. They can also partner with software vendors and consultants who specialize in BIM for precast production planning.
When it comes to precast concrete technology, the benefits of using BIM are clear. From feasibility studies and project planning to precast production planning and real-time tracking of precast elements, BIM can streamline the entire process and ensure the highest quality results. At StruEngineers India Pvt. Ltd., we offer a wide array of BIM services on precast concrete technology, which includes:
– feasibility studies for precast projects,
– precast element design & detailing,
– precast production planning,
– precast project planning,
– real-time tracking of precast elements with quality control and status updates available over our mobile app.
Our in-house BIM platform, StruSoft IMPACT, is one of the best integrated BIM platforms on the market, allowing for a comprehensive and seamless approach to your precast concrete projects.
IMPACT Production Planning helps you PLAN, TRACK, and know the exact STATUS of any type of precast element for any project, any factory, any mould/bed, and any part of the process. It is an ERP system for Precast Production and is unique because every aspect of your processes can be visualized in 3D and in real time.
Let us look at some features of IMPACT Production:
Customizable – Fully customizable to suit your factory setup, production hall, individual casting tables and moulds.
Scalable – Designed for small, medium, and large-sized operations.
Flexible – Helps you to plan all types of precast elements such as solid walls, sandwich walls, double walls, hollow core slabs, double tee slabs, filigrees, columns, and beams.
And how does IMPACT act like an ERP system for precast operations?
IMPACT is a one-in-all system that can manage the following aspects of your precast operations:
- Manage day-to-day factory operations, optimize cast table/bed/mould space, establish, and fulfill production priorities.
- Cloud based, uses SQL database, therefore facilitates efficient collaboration between different stakeholders. No need to call / email people to get information.
- No need to manage spreadsheets that control different sides of the same project and not integrated through all areas of the process.
The full IMPACT Production suite includes the modules – Project Manager, Resource Manager, Cost Estimation, Cast Planner, Erection Planner, Element Control and Custom Reports.
With the Project Manager module, you see in full 3D a single project and drag and drop 3D model data for cast, stack, and transport planning. With the Resource Manager module, you can plan multiple projects for multiple factories for multiple precast element types. The IMPACT Go mobile app allows unlimited number of people (with permissions) to scan QR codes, use the Element Control to change element status, add defects / rejects, assign responsibilities, and view all element info and the best part is that IMPACT can communicate with your conventional ERP software if required.
Conclusion
BIM has the potential to transform the precast production process, offering a range of benefits from increased efficiency to improved quality. By using BIM in precast production planning, precast manufacturers can reduce waste, increase accuracy, minimize errors, and optimize the production process.
To realize the benefits of BIM, precast manufacturers need to invest in training and development programs, develop effective communication strategies and protocols, and partner with software vendors and consultants who specialize in BIM for precast production planning.
By unlocking the power of BIM in precast production planning, precast manufacturers can improve the quality of their precast elements, reduce production time and costs, and contribute to sustainable construction practices.
FAQs: Maximizing Efficiency in Precast Production with BIM Technology
The IMPACT Go mobile app enables stakeholders to scan QR codes on precast elements, update statuses, add defects, and assign responsibilities in real-time. It facilitates seamless communication and collaboration, allowing for efficient tracking and quality control of precast elements. Additionally, IMPACT can communicate with conventional ERP software, enhancing its utility.
IMPACT is cloud-based, uses an SQL database for efficient collaboration, and eliminates the need for spreadsheets by integrating all project aspects. It manages daily factory operations, optimizes space, and establishes production priorities, making it a comprehensive solution for managing precast operations.
IMPACT Production Planning is an ERP system tailored for precast production that allows users to plan, track, and know the status of precast elements in real-time. It is customizable, scalable, and flexible, supporting various precast elements and factory setups. IMPACT visualizes every aspect of the processes in 3D, ensuring comprehensive and seamless project management.
StruEngineers offers a comprehensive range of BIM services for precast concrete projects, including feasibility studies, element design and detailing, production planning, project planning, and real-time tracking of elements with quality control. Their services are designed to optimize the precast production process and ensure the highest quality results.
Building Information Modeling (BIM) is a digital representation of physical and functional characteristics of places. In precast concrete production, BIM streamlines the entire process from feasibility studies and element design to production planning and real-time tracking. It ensures quality, efficiency, and collaboration across all project stages, significantly enhancing the outcome.