These days, many major construction companies in India are actively adopting precast concrete technology in their construction projects. Precast concrete technology is a durable and versatile technology where different elements or panels of concrete are produced under strict quality control measures in state-of-the-art factories by highly trained personnel, with virtually no wastage. There are precast factories whose core business is just manufacturing precast elements and offering them to any client who is interested in using them for their projects. There are on-site precast factories as well, that serve only those construction projects for whom they are set up.
Â
What does precast concrete technology involve ?
Precast concrete technology involves design & manufacturing of custom-designed precast concrete elements such as:
- roof slabs,
- beams
- columns
- wall panels
- partition walls
- load bearing walls
- facades
- preinstalled windows
- staircases
- central core
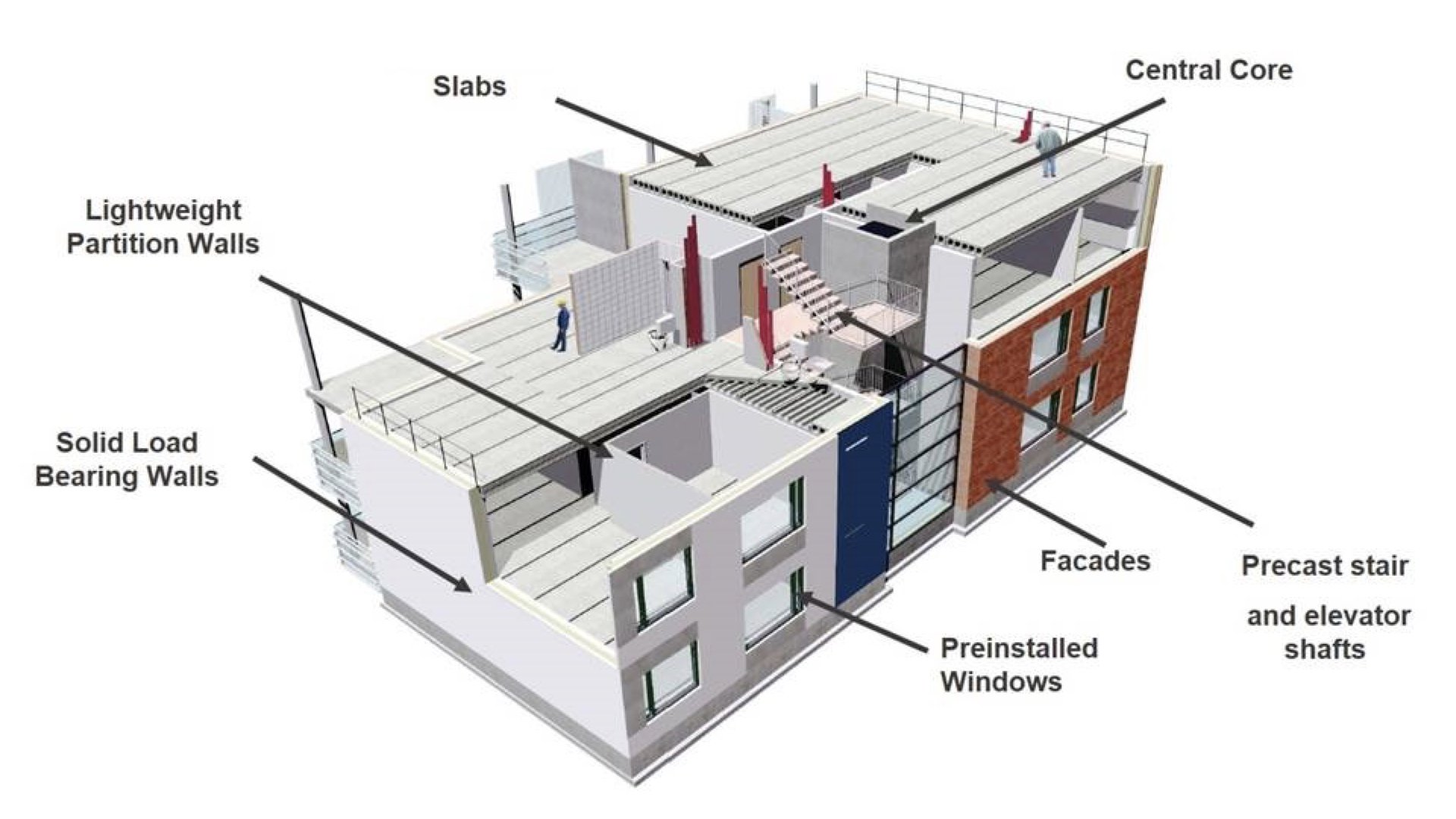
Discover the Future of Construction with StruEngineers!
Are you ready to transform your construction projects with cutting-edge precast concrete technology? Partner with StruEngineers to leverage our expertise in precast design and detailing. Contact us today to learn how we can help you achieve faster, more efficient, and cost-effective construction solutions.
These elements offer flexibility in terms of size and shape with a variety of surface finishes and color options. With precast concrete technology, developers can access a whole new world of creative possibilities in terms of application and design, and there are many options available to engineers & architects to design unique high-quality buildings.
How is it implemented ?
Precast concrete elements are manufactured or cast in a strictly controlled environment as per the required design, with state-of-the-art machinery, by experts. These elements are then erected on site with the help of cranes. The precast elements are then joined together as per specification, with grouts and screeds to provide the required strength and rigidity to the structure.
Major factors that are driving growth of precast concrete technology in India
The key factors are :
1. construction quality
The elements are produced strictly as per design, under controlled conditions; therefore, they are consistent in terms of size, strength, and the finish quality. This is extremely critical for elements that are repeated during construction.
2. speed of construction
Once the elements are designed, it is just a matter of producing them on casts. The curing process is very quick (hours unlike weeks that are required for cast-in-place curing). This advantage really accelerates the construction process as there is literally no waiting time involved in curing of the precast elements. It is estimated that precast concrete technology can save up to 64% of the time taken for similar projects using the old and traditional construction methods and technology.
– Value-for-money
- Near zero material wastage as the entire project is planned well in advance.
- The massive time savings significantly cut down all direct and indirect costs that accrue with passage of time.
– Avoiding large labor force on site
- Precast construction requires very less, but skilled workforce; therefore, all hassles and potential risks associated with managing a large unskilled workforce are eliminated.
– The ability to have large spans using prestressed elements
- By using prestressed slabs, we can have a lesser number of supporting beams.
- Prestressed floor slabs require less thick beams to support them, thereby saving the amount of construction materials required.
Cost Considerations
All the above 5 points highlighted in the above section play either a direct or an indirect role in reducing costs.
Where do we ( StruEngineers ) fit in the precast industry ?
We provide end-to-end solutions like precast elements design, precast elements detailing, precast feasibility study, project planning for precast projects and end-to-end BIM services to precast factories.
Backed by 11 years of experience in this field, we are offering the following services:
To precast manufacturers –
- precast design, precast detailing, precast production, and precast transportation planning
- Using the production planning module, we can plan the mix of elements to be manufactured and the production speed, in tune with the crane capacity, truck capacity and the construction plan.
To builders –
- Precast elements detailing
- Project planning services, which involves ordering the right precast elements at the right time, stacking them in the right sequence at site and erecting them as per the construction schedule.
- 3D simulation & Clash Detection
- 3D simulation – To get an accurate representation of the entire project beforehand.
- Clash detection – to check for errors in the construction design. Clash detection is the process of identifying whether two or more elements overlap or interfere with each other, and check for any instances of misalignment. By using this feature, we can rectify errors at the design stage itself and avoid huge losses in terms of both – time and money during construction.
We have clients from the precast manufacturing industry as well as the precast construction industry, across the globe. Please feel free to check out our client list and the projects page where you will see that we have designed residential & commercial buildings, villas, factories, car parking facilities, mass housing projects and even an underground tunnel for a kids’ play area.
We are happy to invite you to explore our services.
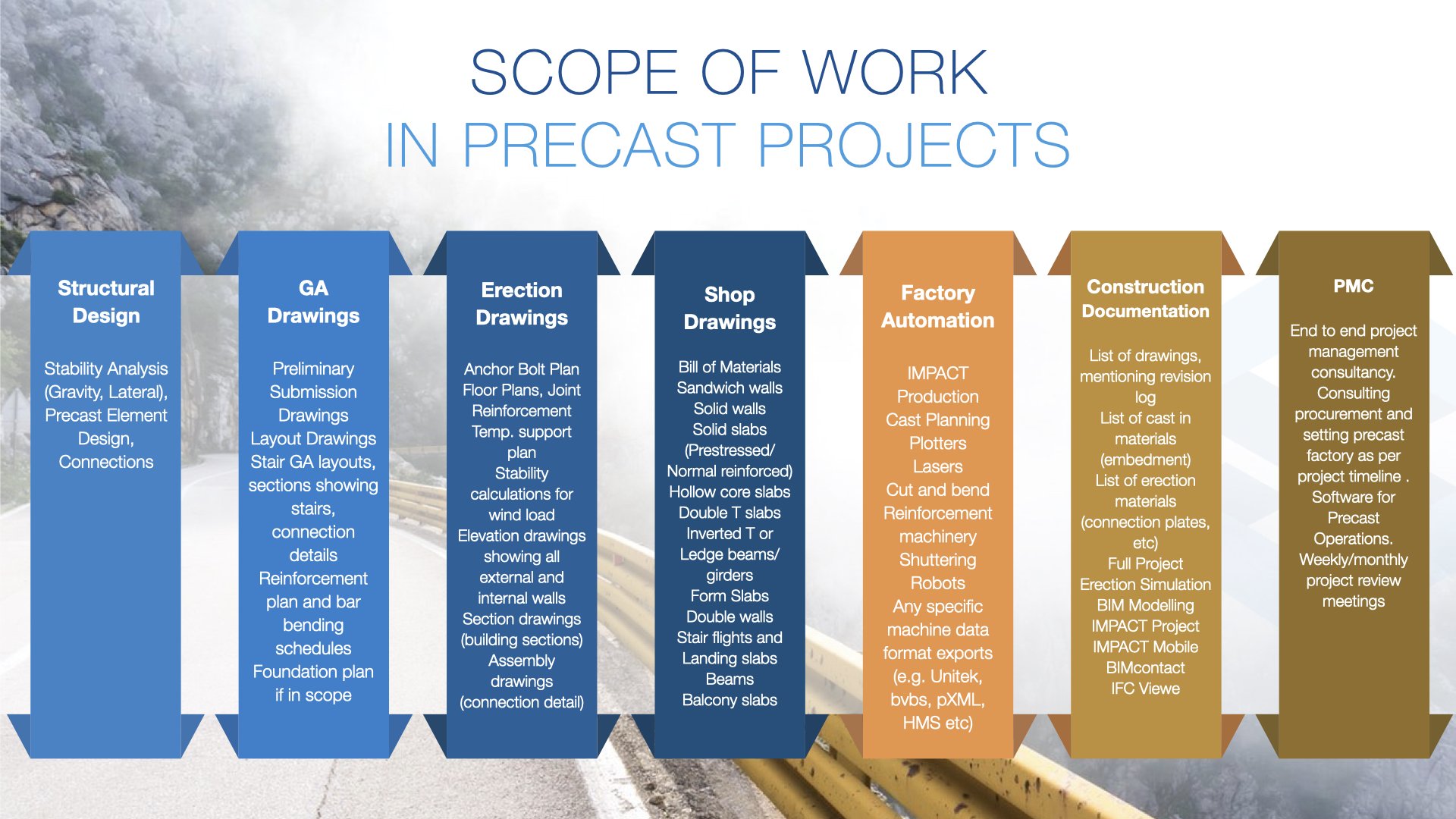
FAQs on the Future of Indian Construction with Precast Concrete Technology
Precast concrete technology can address the housing shortage by enabling rapid construction of high-quality, affordable housing units. Its speed and efficiency can help meet the growing demand for residential buildings, providing a viable solution to urban housing crises.
Challenges include the need for specialized skills and training, initial high investment costs, and the necessity of establishing a robust supply chain for precast elements. However, these challenges can be mitigated through industry collaboration and government support.
Precast concrete technology contributes to sustainable construction by reducing material wastage, lowering energy consumption during production, and enhancing the durability and longevity of structures. This results in a lower overall environmental footprint.
The primary benefits of using precast concrete include faster construction times, consistent quality, reduced environmental impact, and increased safety on construction sites. It also allows for greater design flexibility and precision.
Precast concrete technology is revolutionizing the Indian construction industry by enhancing construction speed, improving quality, reducing labor dependency, and minimizing material wastage. This method offers a more efficient and sustainable approach to building.